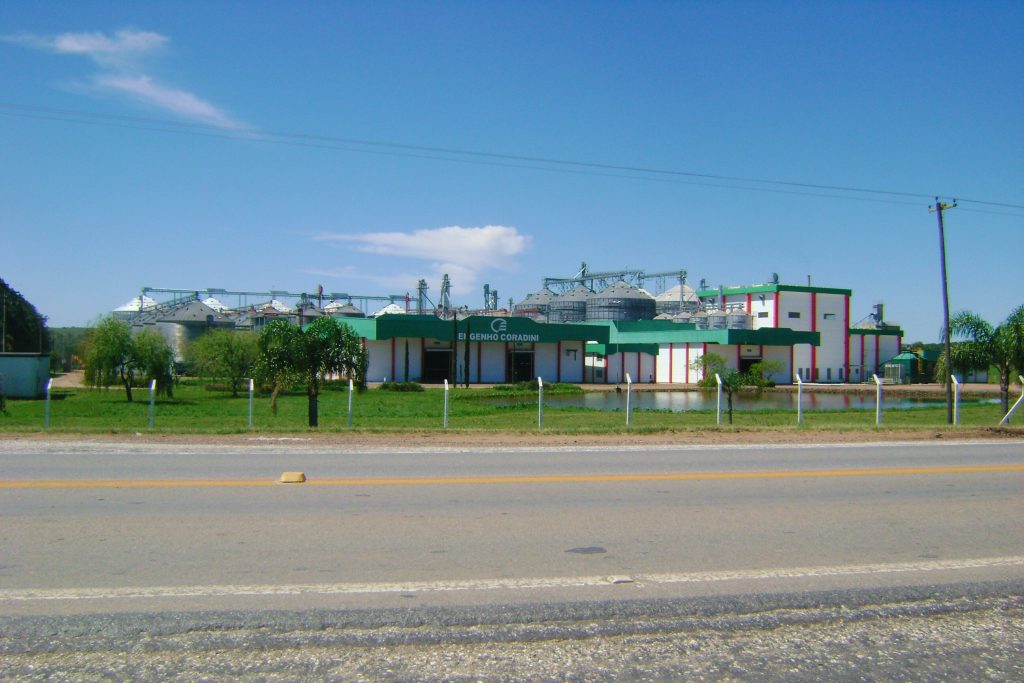
O Engenho Coradini foi fundado em 1955, através da sociedade entre dois irmãos da família Coradini na localidade do 5º distrito de Cachoeira do Sul – RS (atual município de Faxinal do Soturno). Inicialmente, a sociedade era chamada de Coradini & Irmãos Ltda e produzia 1250 toneladas ao ano.
A partir dos anos de 1970, são construídas as instalações do parque industrial na cidade de Dom Pedrito (RS) para acompanhar o desenvolvimento da agricultura no país. Desde então, o Engenho Coradini vem investindo no aumento da capacidade e desenvolvimento da lavoura arrozeira no município, sempre priorizando a mais avançada tecnologia existente no ramo, sem deixar de lado o cuidado com o meio ambiente e a integração com a sociedade. Em 1998, é inaugurada uma nova filial em Dom Pedrito, para a qual a Coradini faz um pesado investimento em controle de qualidade e em automação de processo.
O Engenho Coradini é um grande produtor de arroz, entregando ao mercado anualmente 1,2 milhões de fardos de arroz, que representam aproximadamente 60 mil toneladas de arroz em casca. Além disso, seu parque fabril possui hoje capacidade total para beneficiamento de até 100 mil toneladas do grão. Também é um dos mais modernos engenhos de beneficiamento de arroz do Brasil, sendo um dos primeiros a conquistar a certificação HACCP Codex Alimentarius (Hazard Analisys and Critical Control Points).
Sempre buscando inovação para aumentar sua competitividade, a empresa implementou entre 2009 e 2010 uma planta para produção e beneficiamento de arroz parboilizado, utilizando a tecnologia à vácuo Gariboldi (inédita no Brasil).
Esta planta de produção é englobada por 3 partes distintas, sendo a da produção propriamente dita, com máquinas que foram projetadas e instaladas pelo Studio Técnico Appiani (Milão – Itália), a parte de cogeração de energia, em que a casca do próprio arroz é utilizada para geração de energia, e a parte de beneficiamento, que contempla: o descasque, o brunimento, a classificação e separação dos grãos, o transporte das cascas para o setor de geração de energia, e o transporte dos grãos dentro da planta, desde o silo até o empacotamento.
Escopo de Fornecimento:
- Controlador Programável XC-CPU201-EC256K, do fabricante EATON, com mestre Profibus-DP e Servidor de Dados OPC;
- 5 Remotas de I/O XN-GW-PBDP-12MB, utilizando protocolo Profibus-DP do fabricante EATON;
- 104 Partidas Inteligentes utilizando a rede de comunicação SmartWire DT (Darwin Technology), do fabricante EATON;
- 2 Interfaces Homem Máquina ZB4-504-IF1, utilizando protocolo de comunicação Profibus-DP, do fabricante EATON;
- Licença para Sistema de Supervisão Elipse SCADA;
- Serviços de Engenharia para integração dos equipamentos acima citados com o processo através de desenvolvimento de software para Controlador Programável e Sistema de Supervisão.
Arquitetura:
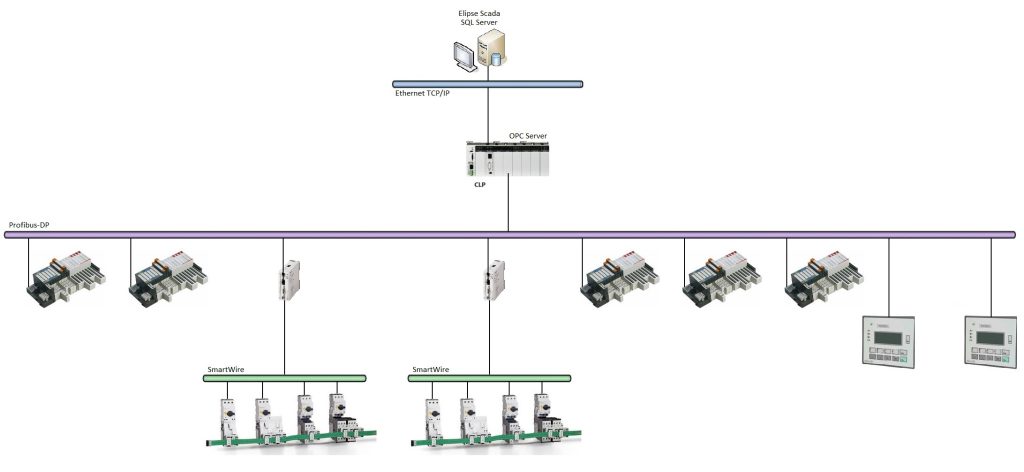
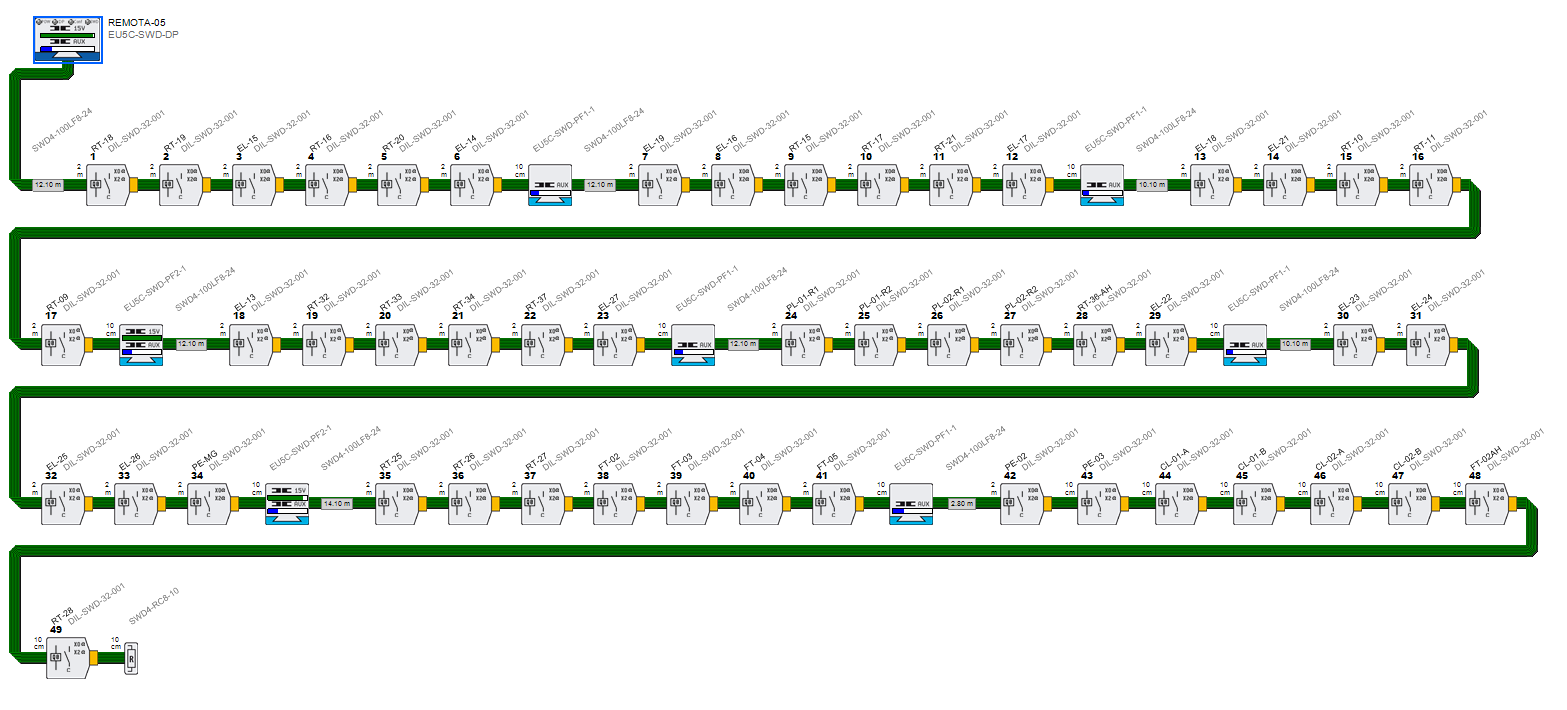
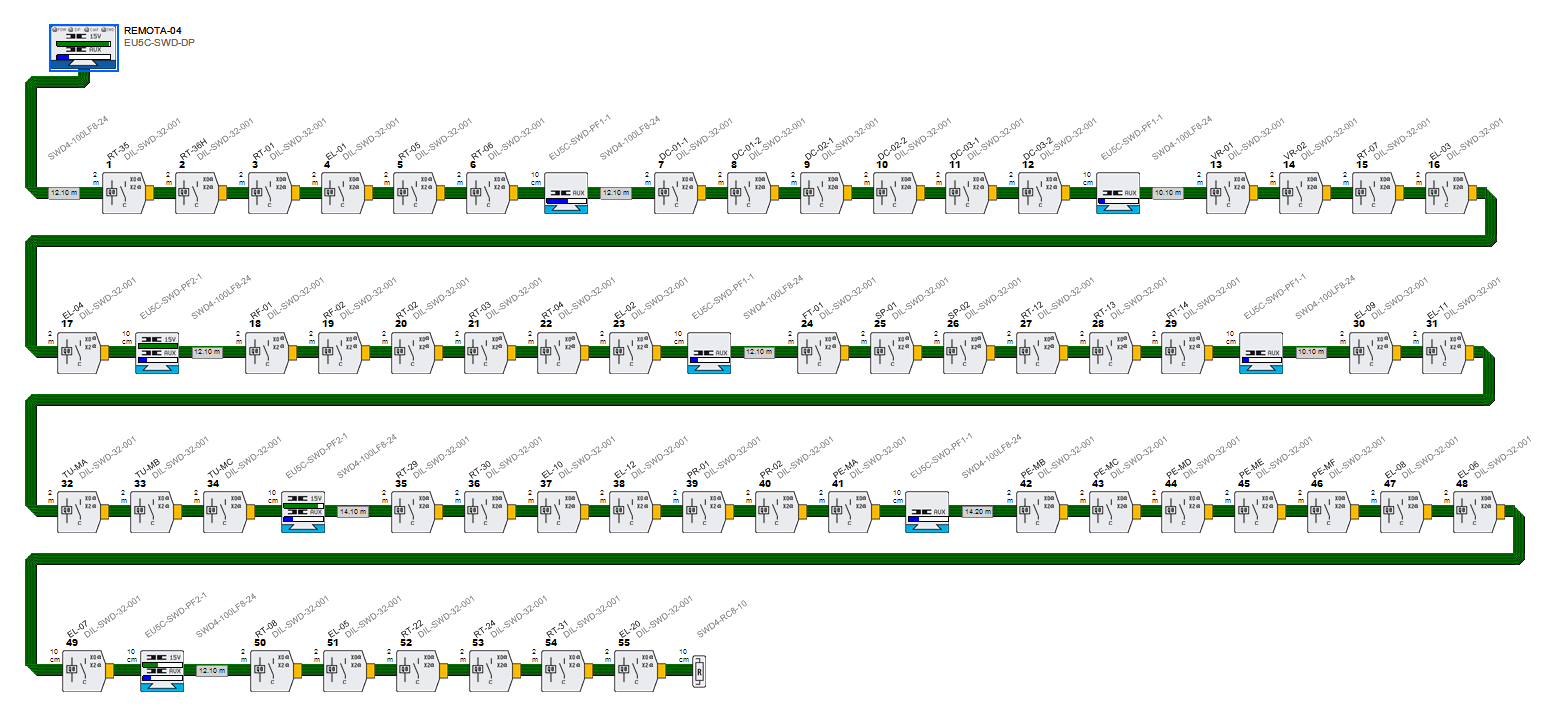
O sistema em números:
- Sistema de Controle da planta para CLP XC-201;
- Sistema de Supervisão SCADA;
- 2 Sistemas de Supervisão para IHM MI4.
Os Softwares:
- Software de Controle:
O software realiza todo o automatismo da planta através do alinhamento de 16 rotas. Nestas rotas estão
envolvidos os motores interligados através de rede Profibus-DP, utilizando Gateways inteligentes EU5C-SWD-DP, e rede SmartWire (DT) controlando um total de 104 motores entre esteiras, roscas transportadoras, elevadores e outros.
Na rede Profibus-DP ainda existem as remotas XION, que recebem informações dos níveis dos silos de
arroz, corrente dos principais motores do engenho, e também a posição e atuação das gavetas para evitar paradas desnecessárias no processo em caso de falha em algum dos motores ao longo da linha.
Também são monitoradas as falhas dos equipamentos utilizando os recursos de diagnósticos dos equipamentos, reduzindo o tempo de manutenção do sistema e assim menos tempo de máquina parada.
- Software de Supervisão SCADA:
O software está interligado à um Servidor do tipo OPC no XC-201, e ambos estão conectados através de rede Ethernet TCP/IP corporativa do próprio Engenho. O sistema permite ao operador o controle total da planta, apresentando em telas sinóticas todo o layout do engenho, bem como a situação atual de cada um dos equipamentos. Estão representados os Descascadores, Câmaras, Módulos Classificadores, Brunidores, Polidores, Elevadores, Roscas Transportadoras, Gavetas e Nível dos Silos. Possui também tela dedicada para gerenciamento de alarmes, onde rapidamente o operador pode identificar o equipamento que apresenta a situação anormal de operação e tomar as ações necessárias para a recuperação da planta ou ainda direcionar o pessoal de manutenção, caso se faça necessário. Possui tela para visualização de eventos históricos, bem como a mudança de estado dos equipamentos principais, ou ainda as variáveis analógicas armazenadas em um banco de dados. Como o Sistema de Supervisão está interligado à rede corporativa, as informações armazenadas são disponibilizadas para o setor de TI da empresa para integração no sistema gerencial.
Abaixo seguem algumas telas do Sistema de Supervisão SCADA:
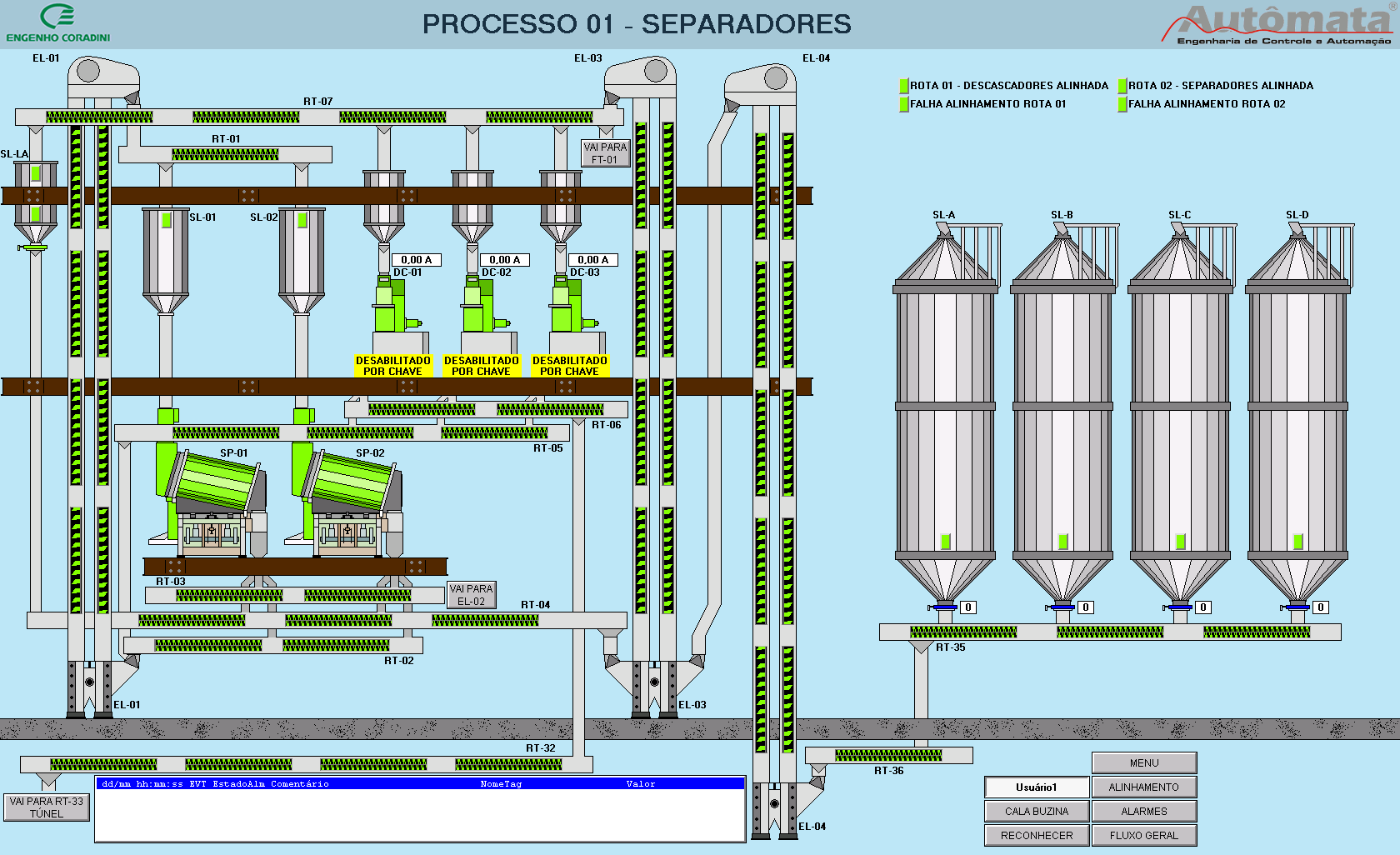
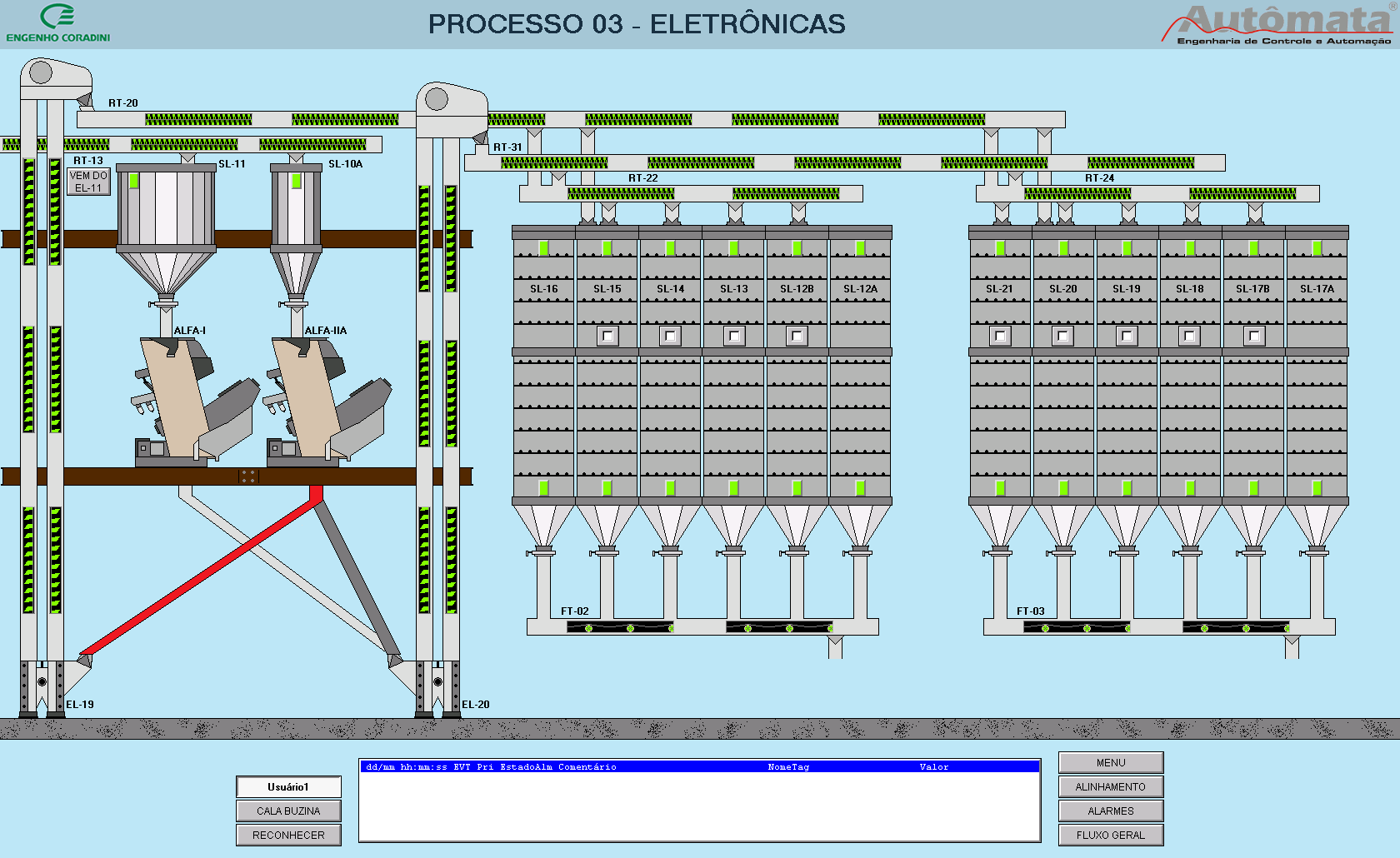
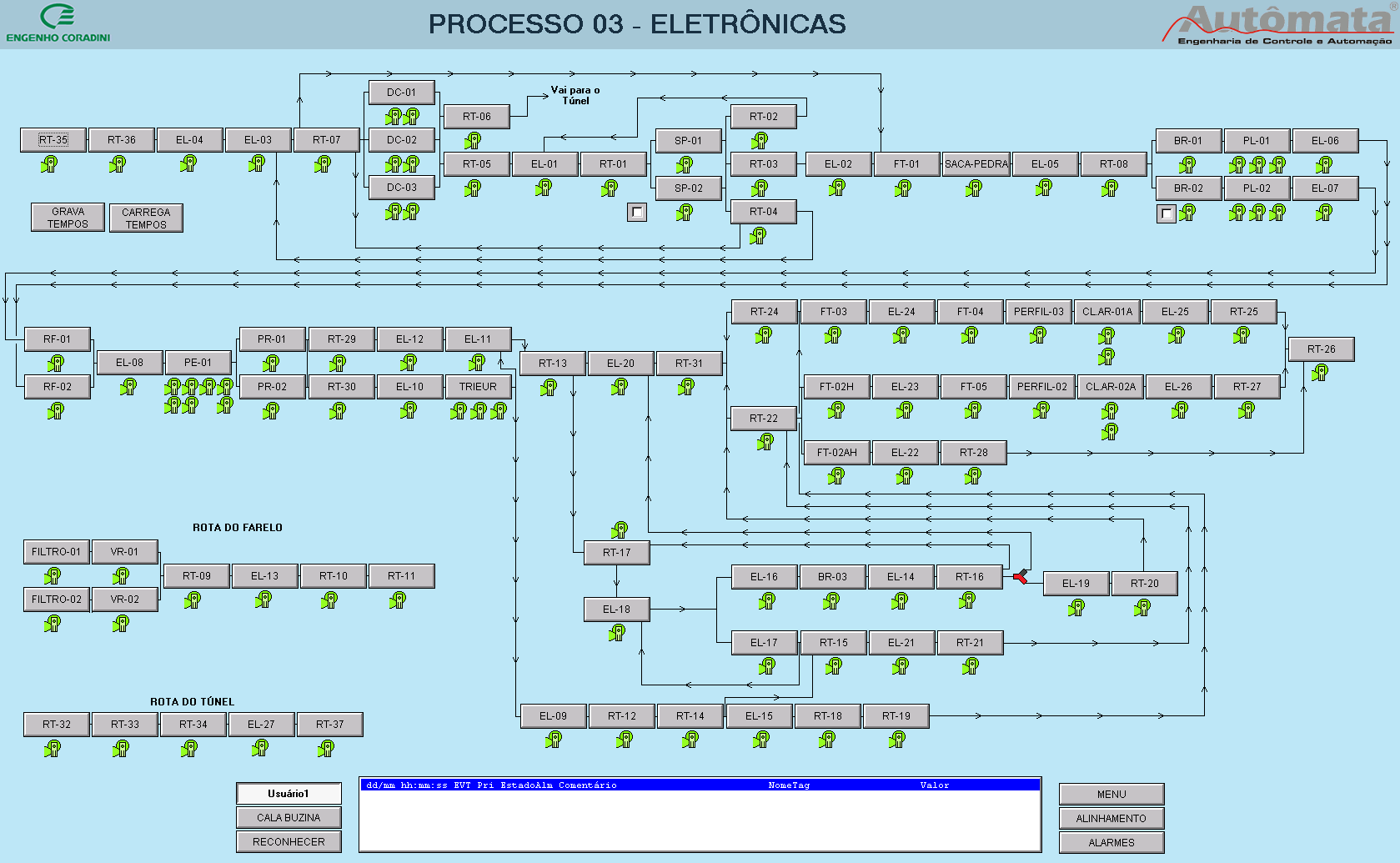

- Sistema de Supervisão IHM:
O software para IHMs, modelo MI4, está distribuído em dois equipamentos alocados em áreas distintas, em que o operador tem acesso apenas as informações pertinentes as áreas nas quais os equipamentos estão instalados e fazem parte. Os equipamentos estão interligados na rede Profibus-DP e recebem todas as informações de campo através do CLP. As IHMs permitem comandos de partida e parada de motores específicos, bem como monitoração de corrente e estado dos mesmos. Também são apresentados alarmes setoriais para cada IHM, onde os mesmos podem ser reconhecidos pelo operador, à distância do sistema de Supervisão SCADA.
Sistema Instalado em 12/2010